The Benefits of Dimple Jackets for Pressure Vessels
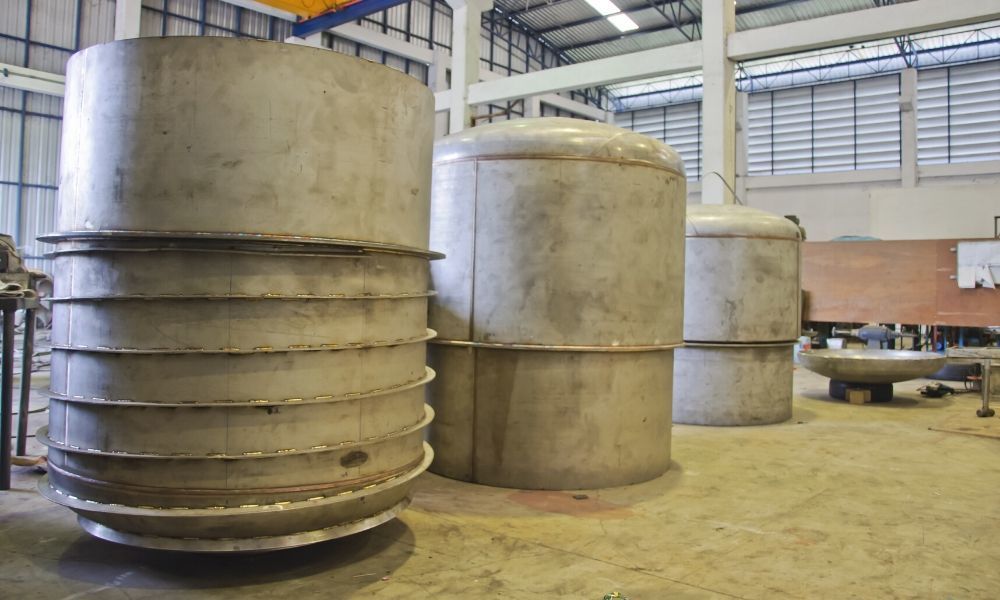
Dimpled jackets improve small and large tanks by providing higher pressure drops for heating and cooling applications up to 300 psi. They typically have a thin-gauge metal plug welded to the vessel shell. The punched areas illustrate a dimpled effect that helps insulate fluids for optimal heating and cooling power. Since dimpled metal sheets compose the dimpled jackets, there are many fabrication options such as radial or straight patterns, rolled sheets with cutout shells, fished heads, flat heads, and cone sections.
These types of jacket vessels use horizontally and vertically placed grooves to impart turbulence to the heating and cooling media. Given that, dimpled jackets offer exceptional heat transfer and liquid distribution, an obvious benefit for pressure vessels. The dimples impart an overall higher heat transfer coefficient and transfer heat with low media via different density contact points. Furthermore, their design makes them a great choice when used for steam or high-pressure applications. Since no increases in structural thickness are needed, fabricators save on money and time with their installation. Based on the ASME’s (American Society of Mechanical Engineers) technical and safety standards, all dimpled jacket vessels use ASME-certified components with the signature ASME code stamp.
At CMPI, we value safety and efficiency in all our stainless steel fabrications. Our dimple jacket heat transfer vessels are designed with exactly this in mind. We provide mechanical dimple jackets with optimal contact points for welding tanks and pressure vessels. Our expert fabrication and installation teams can attach any dimple sheet to your fabrications. Check out our services and products to see for yourself. Then call us and speak to any of our jacketed vessel experts for more information.