A Guide to Stainless Steel Finishes
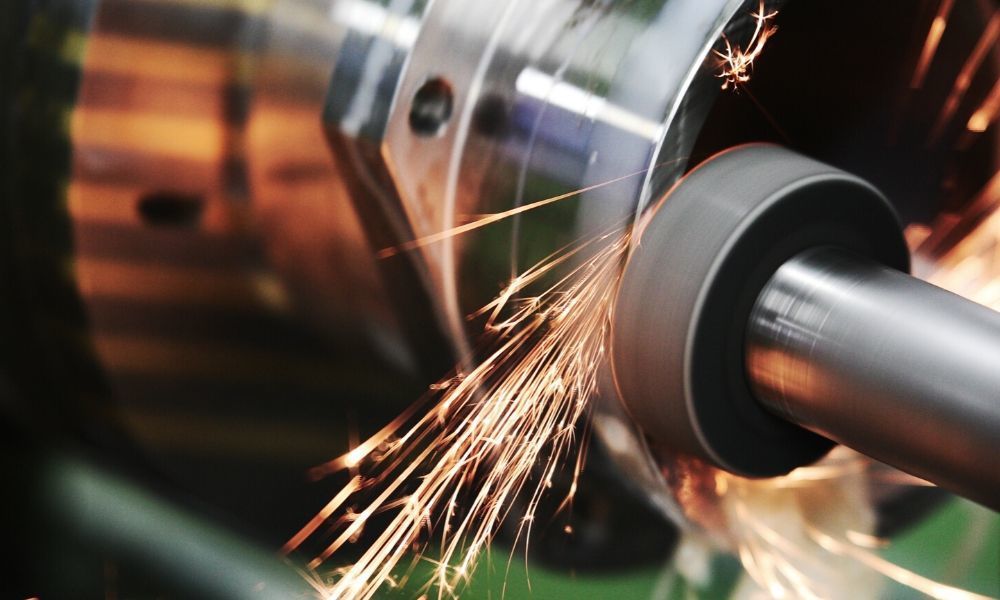
No. 1 Finish
No. 1 finishes require hot rolling to achieve their desired effect. It requires very little finishing, which makes it the roughest finish available. Stainless steel must be heated prior to the rolling process through a heat treatment to produce a uniform microstructure known as annealing. This ensures the stainless steel meets mechanical property requirements. The hot rolling and annealing process results in a dark, varied appearance called a scale. Operators must remove the scale via chemical agents—known as pickling—to provide a higher level of corrosion resistance. The result is a rough, dull, divergent appearance. Due to its final characteristics, No. 1 finishes are uncommon in fabrication applications. You cannot descale or duplicate the finish with hand tools. Nevertheless, No. 1 finishes are commonly used in air heaters, annealing boxes, boiler baffles, furnace parts, gas turbines, or other applications that don’t require any reflection.
No. 2B Matte Finish
No. 2B is one of the most common stainless steel finishes used today. It’s a cold roll finish that’s non-reflective, smooth, and has good flatness. Often, the surface has a smooth, reflective grey matte finish, meaning it’s dull and unreflective in appearance. This makes it perfect for applications requiring a basic and unaesthetic stainless steel surface finish. With that, 2B finishes are often the least expensive available option. In this case, the thickness can range based on skin passing capacity. To produce a No. 2B finish, stainless steel is cold rolled through a special roller. This produces a smooth, less pitted surface. Then, the surface is softened and descaled in an acid solution. Finally, it passes through polishing rolls for further smoothness. The most common applications for No. 2B finishes include chemical and pharmaceutical equipment, laundry and dry cleaning, refrigeration, and sewage.
No. 3 Brushed Finish
No. 3 finishes are a 120-grit option. They obtain a 120-grit abrasive through a one-directional course. This type of finish is also known as grinding, roughing, or rough grinding given its coarse, preliminary finish. The intermediate polished finish ensures a peel-off protective covering on one side of the sheet. Using an initial 50- to 80-grit abrasive to achieve a final 120-grit abrasive, No. 3 finishes require mechanical or gradual finer polishing techniques via special coils or rolls. The resulting polishing lines indicate linear grain pattern with a roughness average (Ra) of less than or equal to 40 micro-inches and a moderate reflective finish. Operators must use short strokes in an elliptical motion to create these short grain patterns. No. 3 finishes are commonly used in food production and food service. This includes brewing equipment, food processing, kitchen equipment, and scientific apparatuses.
No. 4 Brushed Finish
Like No. 3 finishes, No. 4 finishes are also characterized by short, uniform parallel polishing lines on the stainless steel sheet surface finish chart. They typically require a No. 3 finish with gradually finer abrasives. This final finish can end anywhere between 150- and 320-grit. Typically, as the grit number increases, polishing lines are finer and the reflective finish is greater. No. 4 finishes show an Ra of 25 micro-inches or less with a highly reflective finish. Similar to No. 3 finishes, No. 4 finishes are used for general purposes. The uses for No. 4 finishes are similar as well, as No. 4 finishes are widely used for kitchen and restaurant equipment, food processing, dairy equipment, hospital surfaces, highway tank trailers, control panels, and water fountains.
No. 7 Finish
No. 7 finishes are defined by their high reflection and mirror-like appearance. To reach this state, a No. 4 finish is polished with a 320+ grit and buffed until fine polishing lines are noticeable. The buffing process can take up to 10 minutes on different stainless steel finishes. Also, existing grit lines are kept minimal. An observer can see the polishing lines from several feet away. No. 7 finishes are used for various applications, but the most common are column covers, ornament trim, and wall panels.
No. 8 Mirror Finish
Like No. 7 finishes, No. 8 finishes are also defined by their high reflection and mirror-like appearance. They are the most reflective stainless steel finishes available by ASTM standards. In a No. 8 finish, buffing continues for an additional five to ten minutes until grit lines are nearly invisible. Polishers reach this desired mirror-like appearance simply through longer polishing time. Finishing time determines the distance needed to spot imperfections and grit lines. Having longer polishing times means lesser distances, which ultimately results in near-perfect mirror-like appearances. Given their highly reflective surface, No. 8 stainless steel sheet finishes have a lot of notable everyday applications. They are used in press plates, signs, wall panels, column covers, mirrors, and reflectors. More so, the notable Cloud Gate in Chicago, Illinois uses a No. 8 stainless steel finish. Also known as “The Bean” amongst locals, this attraction draws hundreds of daily spectators who take pictures and observe their reflections in the steel finish.
Bright Annealed (BA) and Temper Rolled (TR)
Last in this guide to stainless steel finishes are Bright Annealed and Temper Rolled finishes. BA finishes are often confused with No. 8 finishes, but they are different as they do not provide a clear finish. While No. 7 and No. 8 finishes have a mirror-like quality, the annealing process of BA finishes does not produce the scale on the stainless steel surface finish. This results in a reflective finish without further processing. Temper rolled finishes are used for strong mechanical properties. Stainless steel rolls are polished until the result is an even finish. For the best stainless steel polishing services in Springfield, MO, call us at Custom MFG & Polishing (CMPI). We offer polishing for all stainless steel applications like sheets, plates, pipes, tubes, round and flat bars, and custom fabrications. Through our rigorous quality standards, we guarantee the best carbon-free polishing for any stainless material. No matter the Ra or grit, we offer finish options from No. 3 to No. 7. Contact us today to learn more about our services from any of our expert service technicians