14 Different Pipe and Tube Manufacturing Challenges
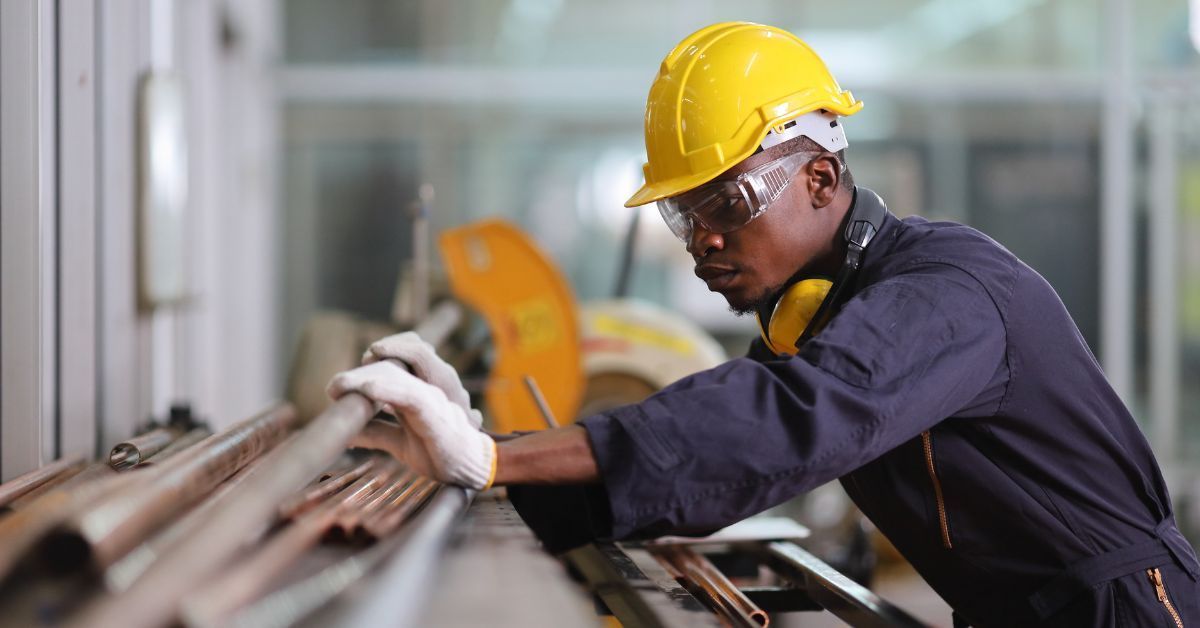
Specialized stainless steel components are common in the aerospace, automotive, and construction industries. However, the production process is complex and requires precision engineering, extensive material expertise, and ongoing innovation.
Professionals in production often face challenges—equipment failures, supply chain delays, communication breakdowns, quality control issues—that can disrupt workflows and negatively impact efficiency. These obstacles require proactive strategies to overcome.
Understanding the causes of these challenges is the only way to find effective solutions, whether it’s better planning, adopting new technologies, or improving team collaboration. It sets your teams up for success!
By addressing these issues head-on, professionals can streamline operations and achieve better results in their production processes.
1. Material Selection
Choosing the ideal stainless steel grade for a project is the first step. Balance each application with the qualities you need from your materials, including strength, corrosion resistance, and workability. Selecting the wrong material could compromise performance or increase production costs.
To make the best choice, consider exposure to moisture, chemicals, or extreme temperatures. Consult material specialists, and evaluate the stainless steel grade’s performance in similar applications. This will guarantee the selected material meets your functional and budgetary requirements.
2. Raw Material Quality and Sourcing
The quality of raw materials directly affects the final product. However, sourcing certified stainless steel that meets regulatory and application standards can be tricky. Once you have the material, inconsistent quality or delays may add complexity to production timelines.
Working with reliable suppliers who prioritize quality and efficiency will give you peace of mind and support smooth operations. Additionally, regular quality checks during production can help you identify and address potential issues. Investing in high-quality raw materials promises better durability, performance, and customer satisfaction.
3. Precision in Dimensional Tolerances
Many manufacturers require close tolerances for custom stainless steel tubing to guarantee the product functions as intended. Deviations as small as a fraction of a millimeter can lead to alignment problems or poor performance and hinder the manufacturing process.
Achieving precise tolerances requires advanced manufacturing techniques and rigorous quality control. Every step of the process, from selecting the right materials to employing specialized tools, is critical for producing tubing that meets your specifications and performs well. Some of these products could be part of the next space expedition!
4. Uniform Wall Thickness
Achieving a consistent wall thickness across the length of a tube can be difficult. Thinning or bulging can occur during high-pressure applications. These issues result in wasted material and failed quality checks, which cost you and your client money.
Advanced manufacturing techniques, such as precision extrusion and automated quality monitoring, are a must to address these challenges. These methods help you detect irregularities early in production. The final product should meet the specifications and not go to waste.
5. Welding Challenges
The precision required for seamless and welded tubing adds complexity, particularly when aiming for defect-free welds. Poor-quality welding can weaken the tube’s structural integrity, which compromises safety and performance in real-life environments. Quality control and advanced inspection techniques will guarantee that your welds are up to snuff.
6. Surface Finish Quality
A flawless finish is non-negotiable for pipes and tubes used in healthcare and food processing. Achieving defect-free finishes, especially for tubes with non-standard shapes or sizes, requires advanced polishing techniques and skilled labor.
A smooth surface finish supports cleanliness and improves durability and resistance to corrosion. Precision polishing is critical for maintaining product quality.
7. Customization Complexity
No two projects are the same, and customization can produce manufacturing challenges. The need for different sizes, shapes, and bends in tubes and pipes often stretches production capabilities and requires innovative solutions that balance customer needs with operational feasibility.
Advanced technologies, such as automation and 3D modeling, are helpful for streamlining these processes. By adopting these tools, manufacturers can meet customization demands while maintaining efficiency and quality.
8. Tooling Limitations
Many projects demand specialized or customized tooling, which can delay production schedules. Frequent modifications to tools come with a financial burden that challenges cost management strategies. Finding efficient and flexible solutions is crucial to minimize delays and control expenses.
9. Heat Treatment and Annealing
Heat treatment helps manufacturers achieve the desired mechanical properties. However, improper application can warp materials, cause oxidation, or make the material too brittle.
You’ll need quality control for this process. Advanced monitoring technologies can guarantee precision and minimize errors during heat treatment.
10. Preventing Material Contamination
Maintaining a sanitary environment during the manufacturing of medical and food-grade tubes is non-negotiable. Contamination can occur at any stage, from handling to processing, and might lead to costly recalls or rejected shipments.
Stringent hygiene protocols and regular equipment maintenance can prevent issues. Investing in quality control measures guarantees product safety and protects your brand reputation.
11. Cracking and Ductility Issues
Cracking is a big problem during forming or welding. Balancing the ductility and strength of a tube, especially for custom designs, requires careful material selection and control of forming techniques. Testing and quality assurance are essential for meeting performance standards.
12. Testing and Quality Control
Perform a thorough inspection for flaws, such as internal voids or cracks. You may need to employ ultrasonic or X-ray testing, but they can be expensive and time-intensive, especially when inspecting tubes with complex geometries.
Scientists and manufacturers are developing advanced inspection methods to provide faster and more cost-effective solutions. These innovations aim to improve accuracy while reducing downtime during the inspection process.
13. Maintaining Industry Standards
Compliance with ISO, ASTM, and other certifications is necessary for production. Staying updated with evolving standards while maintaining audited processes and strict documentation is a resource-intensive challenge.
However, achieving compliance promotes quality and safety while building trust with clients and stakeholders. Investing in streamlined systems and expert guidance can facilitate navigating these requirements.
14. Production Efficiency and Costs
Customization makes scaling production more difficult. Labor costs, energy use, and material waste further complicate achieving cost efficiency. Streamlining processes to reduce these issues requires constant monitoring and adaptation.
Solutions and Innovations in Manufacturing
Despite these challenges, modern solutions are transforming the manufacturing landscape. Advanced welding techniques and automated tool customization improve precision and reduce timelines. In addition, 3D printing and CAD allow for rapid prototyping, which produces refined designs before production.
Quality assurance and real-time monitoring help manufacturers meet standards. Partnering with reliable suppliers for premium materials also eliminates risks associated with subpar raw inputs. CMPI delivers dependable stainless steel solutions by blending advanced capabilities with customer-centric designs.
Meeting Demands in Pipe and Tube Manufacturing
Addressing these manufacturing challenges with different pipes and tubes is key to guaranteeing quality, reliability, and customer satisfaction. Developing new processes and investing in innovative technologies allows you to navigate these hurdles and drive efficiency.
By working with CMPI, you can streamline production and meet industry standards. From custom designs to expert polishing, we offer a one-stop solution that meets your project requirements.
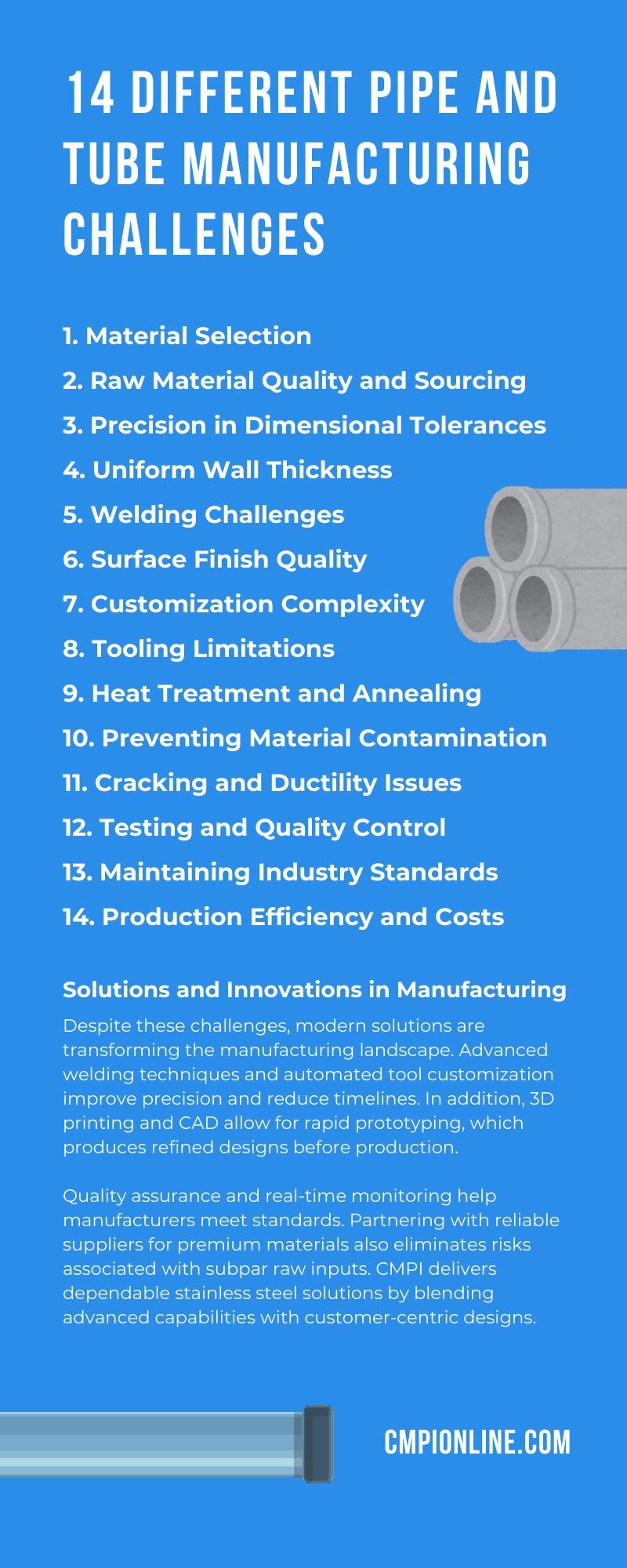