Complete Breakdown of Metallurgy for Stainless Steel Plates
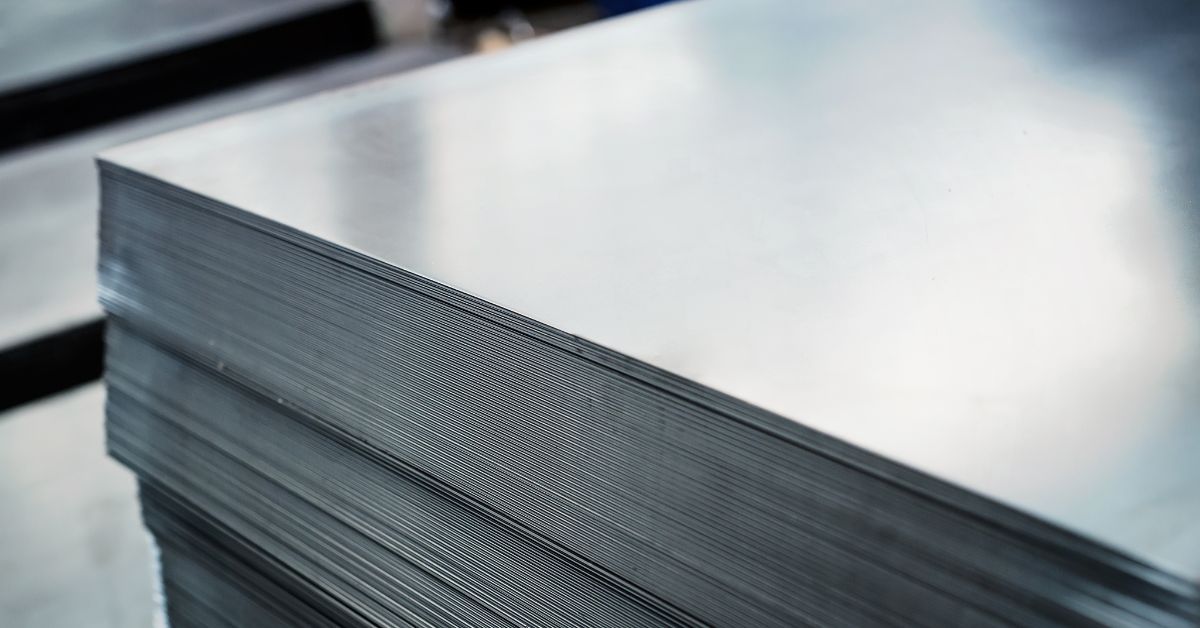
Stainless steel plates offer durability, corrosion resistance, and unmatched versatility compared to most building materials. Metallurgy transforms raw elements into alloys with distinct compositions and properties.
This breakdown of metallurgy for stainless steel plates is the key to understanding how technicians create, refine, and apply these plates. Explore their production processes, types, applications, and emerging trends to grasp the depth of this metal.
How Metallurgy Affects Stainless Steel
Stainless steel contains at least 12 percent chromium, which forms a passive protective layer that resists oxidation and corrosion. Scientists add other elements, such as nickel, molybdenum, and carbon, to enhance mechanical strength and chemical stability.
These metallurgical processes directly influence the performance of stainless steel, especially with polished stainless steel sheets for architectural and industrial applications. Forging, alloying, and heat treatment are important techniques in refining its distinctive properties, including high strength and resistance to harsh environments.
Key Metallurgical Processes in Stainless Steel Production
The production of stainless steel plates involves multiple stages—melting, casting, heat treatment, and precision finishing—to refine and strengthen raw materials for industrial use.
Melting and Casting
The creation of stainless steel begins in powerful electric arcs or induction furnaces. Technicians melt raw iron and alloying elements, like chromium and nickel, together at extremely high temperatures.
Then, they cast molten metal into slabs, the first form of the stainless steel plate. Precision during this step guarantees consistency in the material’s composition, which is critical for its corrosion resistance.
Hot Rolling and Cold Rolling
Next, technicians subject slabs to hot rolling in order to eliminate pores and refine the grain structure. This high-temperature process improves ductility and reduces the likelihood of fractures. Cold rolling, a subsequent process, further smooths the surface and enhances the precision of the final product’s dimensions.
Annealing and Heat Treatment
Annealing involves heating the rolled material, then slowly cooling it to relieve internal stresses and refine its microstructure. For controlled properties—tensile strength and hardness—additional heat treatments, such as tempering, may occur. These processes make stainless steel ideal for chemical processing containers or medical equipment.
Pickling and Passivation
In post-production, stainless steel undergoes pickling to remove surface impurities, including scales and oxides. Following this, passivation treatments restore and enhance the protective chromium-rich layer, which solidifies the material’s resistance to corrosion. These final steps guarantee stainless steel plates are functional and look good.
Types of Stainless Steel
Stainless steel falls into distinct categories, offering unique benefits for industrial and commercial applications. Foundry workers determine these categories by their composition and properties.
Austenitic Stainless Steel
This widely used type has excellent corrosion resistance, ductility, and non-magnetic properties. Grades 304 and 316 excel in environments exposed to moisture or mild chemicals. Their applications include food processing equipment, kitchen surfaces, and pharmaceutical industries.
Ferritic Stainless Steel
Ferritic stainless steel is magnetic and moderately resistant to corrosion. Additionally, it has a low nickel content, and it’s cost-effective. It is useful in automotive exhaust systems and decorative components due to its appealing finish.
Martensitic Stainless Steel
Offering high hardness and strength, martensitic steel is heat-treatable and corrosion-resistant in mild environments. Popular grades, such as 410 and 420, are ideal for surgical instruments and high-stress mechanical parts.
Duplex Stainless Steel
Combining the advantages of austenitic and ferritic types, duplex steel is exceptionally strong and resistant to stress corrosion cracking. Professionals in the oil and gas industry find this metal indispensable for applications requiring durability under extreme conditions.
Precipitation-Hardening Stainless Steel
Through controlled heat treatments, this type achieves exceptional strength while maintaining impressive corrosion resistance. It is useful in aerospace and defense applications because it does not compromise the performance of components.
Properties and Applications of Stainless Steel Plates
Stainless steel plates have properties that make them perfect for high-performance and aesthetically pleasing applications. Their exceptional resistance to corrosion and durability promises long-lasting reliability, even when exposed to the elements.
The chromium content forms a self-repairing oxide layer that protects the plates from rust and discoloration. Strength and toughness remain consistent despite exposure to different temperatures to enhance their reliability for structural components. Finally, the smooth surface finish of stainless steel plates makes them easy to clean for charming architecture and designs.
These properties lend themselves to diverse applications. Architects can use stainless steel plates for building façades and canopies, while professionals in the chemical and food industries rely on them for storage tanks and processing systems. Lightweight plates can become aerospace and automotive components.
Challenges in the Metallurgy of Stainless Steel Plates
Despite its many advantages, producing and utilizing stainless steel poses challenges. Fluctuating prices of alloying elements, such as chromium and nickel, can drive up material costs. During production, it can be difficult to achieve a consistent and uniform grain structure, particularly during rolling and heat treatment processes. Finally, improper passivation or exposure to highly corrosive agents can lead to localized corrosion, such as pitting or crevice corrosion.
Environmental sustainability is another concern, given the energy-intensive processes involved in metallurgy. Forward-thinking manufacturers are trying to alleviate these issues through innovations in recycling and energy-efficient production methods.
Future Trends in Stainless Steel Metallurgy
Scientists and technicians are driving the future of stainless steel through advances in technology and a growing demand for sustainable solutions. Emerging metallurgical techniques, including machine learning-driven alloy design, reduce production errors and optimize material properties.
In order to adopt sustainable practices, manufacturers are focusing on reducing their carbon footprints through recycling materials. Additionally, renewable energy suppliers require custom stainless steel plates for specialized infrastructure.
Shaping Industries With Stainless Steel Plates
The evolving metallurgy for stainless steel plates highlights its role in defining modern industries. Its versatility continues to influence the construction, automotive, and chemical sectors. Advances in production methods, sustainable practices, and innovative alloy compositions will further expand its scope.
CMPI is a trusted name in stainless steel polishing, offering high-precision sheets tailored to diverse specifications. Partnering with us means your projects meet technical requirements and achieve quality and precision. The bright future of stainless steel reflects the resilience and ingenuity of the industries it serves.
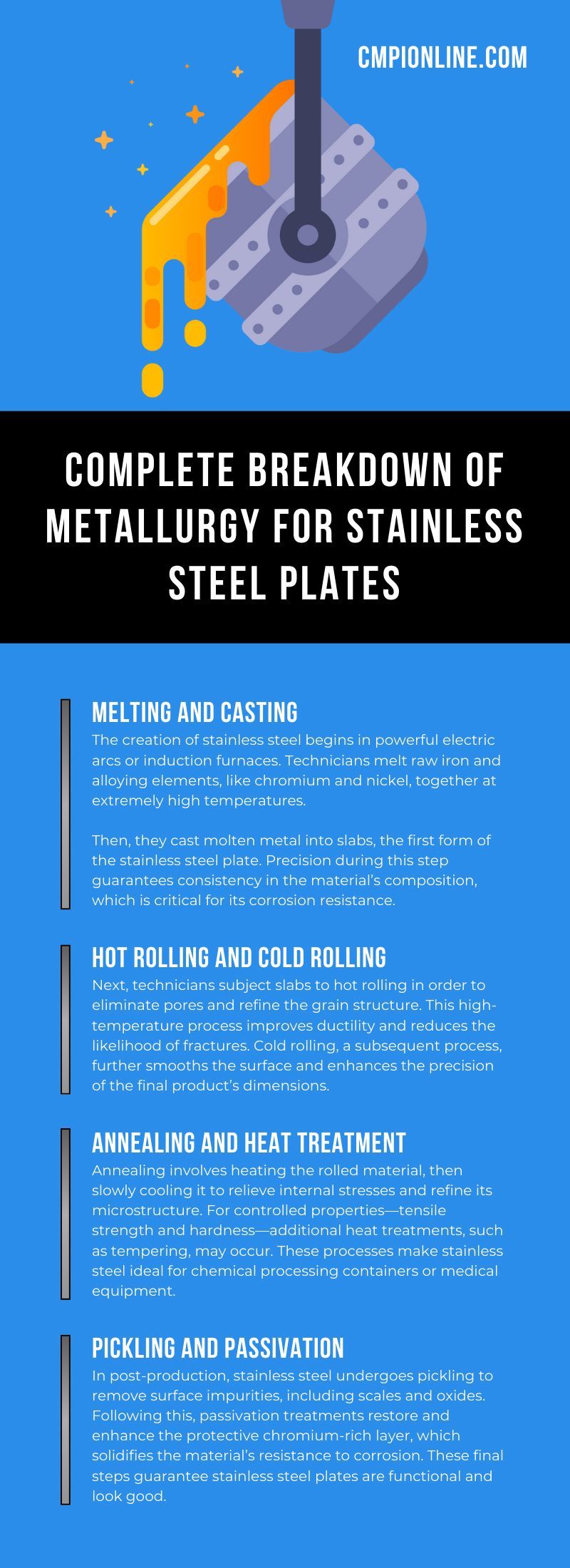