A Guide to Non-Destructive Welding Testing Methods
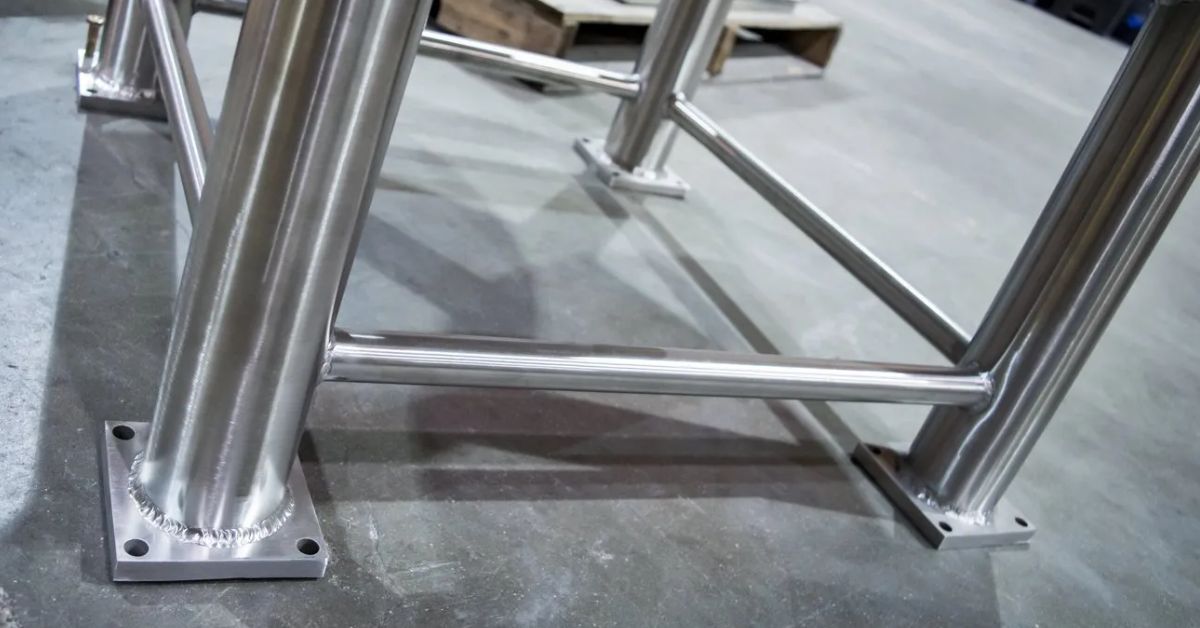
Welding is a crucial component of many industries, from construction to automotive to aerospace. Ensuring the quality and integrity of welded structures is essential for safety and performance—this is where non-destructive welding testing (NDT) comes into play, allowing for the inspection of welds without damaging them. Learn about the various techniques available with this guide to non-destructive welding testing methods.
Understanding Non-Destructive Welding Testing
Non-destructive welding testing refers to a variety of techniques used to evaluate the properties of a material, component, or system without causing damage. These methods are indispensable for detecting flaws and ensuring the reliability of welded structures. This makes it possible to maintain high standards of quality while avoiding the costs and downtime associated with destructive testing. By identifying issues early, NDT helps prevent potential failures and extends the lifespan of structures.
The Importance of Non-Destructive Testing in Welding
Non-destructive testing is essential in welding for a few reasons. First, it ensures safety. Welded structures must withstand various stresses and strains, and any flaw could lead to catastrophic failures. NDT helps identify these flaws before they become serious problems.
Secondly, NDT upholds quality standards. Industries such as aerospace, automotive, and construction rely on high-quality welds. Non-destructive testing allows for continuous monitoring and evaluation, ensuring that each weld meets the required specifications.
Lastly, non-destructive testing is cost-effective. By identifying defects early, NDT prevents costly repairs and rework. It also reduces the risk of project delays caused by structural failures. Consequently, NDT saves money and enhances productivity.
Common Non-Destructive Testing Methods
There are several non-destructive testing methods used in welding, each with unique advantages and applications. Let’s take a closer look at some of the most common techniques.
Visual Testing
Visual testing is the simplest and most straightforward method. Inspectors use their eyes, often aided by magnifying devices, to examine each weld for surface defects such as cracks, porosity, and incomplete fusion. While it may seem basic, visual testing is highly effective for detecting obvious flaws.
This method is often the first line of defense in quality control. Inspectors can quickly identify issues that may require further, more detailed examination. Visual testing is cost-effective and easy to implement, making it a staple in welding inspection.
However, visual testing has its limitations. It cannot detect subsurface defects or very small flaws that might be critical. Therefore, it is often used in conjunction with other NDT methods to provide a comprehensive assessment.
Radiographic Testing
Radiographic testing involves using X-rays or gamma rays to create images of the weld. These images, known as radiographs, reveal internal defects such as voids, inclusions, and cracks. Radiographic testing is highly effective for inspecting complex welds and ensuring the integrity of critical structures.
The process involves placing a radiation source on one side of the weld and a detector on the other. The radiation passes through the weld, and any defects appear as dark spots on the radiograph. This method provides a detailed view of the internal structure, making it invaluable for quality assurance.
However, radiographic testing requires specialized equipment and trained personnel. It is also relatively time-consuming and can be expensive. Additionally, you must take specific safety precautions to protect workers from exposure to radiation.
Ultrasonic Testing
Ultrasonic testing employs high-frequency sound waves to detect defects within welds. A transducer sends sound waves into the material, and it records any reflections from discontinuities. This method is highly sensitive and capable of detecting small, subsurface defects.
Ultrasonic testing is versatile and used on a variety of materials and welding types. It provides rapid results and does not pose any health risks to inspectors. The equipment is portable, making it suitable for field inspections.
Despite its advantages, ultrasonic testing requires skilled operators and proper calibration. Interpretation of the results can be complex, and some materials may attenuate the sound waves, reducing the accuracy of the test. Nevertheless, it remains a popular choice for many applications.
Magnetic Particle Testing
Magnetic particle testing is another widely used NDT method. It involves applying a magnetic field to the weld and then dusting the surface with iron particles. Any surface or near-surface defects create interruptions in the magnetic field, causing the iron particles to accumulate and form visible indications.
This method is quick and effective for detecting cracks, seams, and other surface flaws. It is popular in industries such as automotive, aerospace, and manufacturing, where ferromagnetic materials are common.
However, magnetic particle testing only recognizes ferromagnetic materials and cannot detect subsurface defects. It also requires proper surface preparation and can be messy. Despite these limitations, it is a valuable tool in the NDT arsenal.
Dye Penetrant Testing
Dye penetrant testing is a versatile method for detecting surface defects in welds. It involves applying a liquid dye to the weld surface and allowing it to penetrate any cracks or defects. After a specified dwell time, the excess dye is removed, and a developer is applied to draw the dye out of the defects, making them visible.
This method is simple and effective for detecting surface defects. It is suitable for a wide range of materials and provides clear, visual indications of flaws. Dye penetrant testing is cost-effective and easy to implement.
However, like visual testing, dye penetrant testing can only detect surface defects. It also requires proper surface preparation and cleaning. Despite these limitations, it is an essential method for ensuring the quality of welds.
Future Innovations in Non-Destructive Testing
The field of non-destructive testing is constantly evolving, with new technologies and methods emerging regularly. Future innovations hold the promise of even greater accuracy, efficiency, and ease of use.
One area of development is in the use of advanced imaging techniques. High-resolution imaging technologies, such as digital radiography and computed tomography, are becoming more accessible and affordable. These technologies provide detailed images of welds, improving the detection of defects.
Remote and automated testing are also on the rise. Drones and robotic systems can perform inspections in hard-to-reach or hazardous areas, reducing the risk to human inspectors. These systems can also operate continuously, providing real-time monitoring and assessment.
Ensuring the Quality and Safety of Welded Structures
Non-destructive welding testing is an essential tool for ensuring the quality and safety of welded structures. By understanding the different methods, their advantages and limitations, and best practices for implementation, you can make informed decisions for your projects.
Whether you are a seasoned professional or new to the field, this guide to non-destructive welding testing methods offers insights and solutions for maintaining high standards of quality and safety. Explore the various methods available and consider incorporating them into your workflow to improve your welding projects.
At CMPI, we offer a variety of welding and fabrication services to fit your specific requirements. Browse our selection of heat transfer surfaces to find the right solution for your project, or contact us today to learn more.
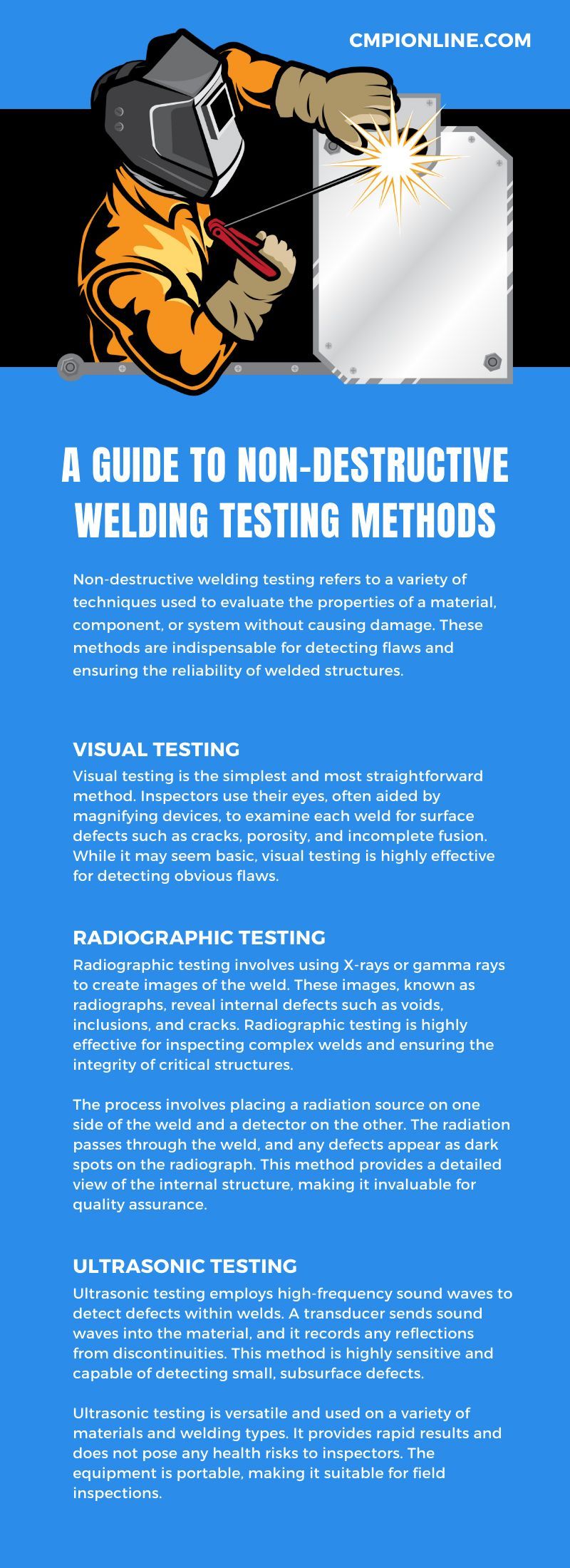